Golden weld performed on-site with robot
In close cooperation with Equinor, Effee Induction have performed a ground-breaking robotised “golden weld” operation that could revolutionise the way maintenance is done offshore.
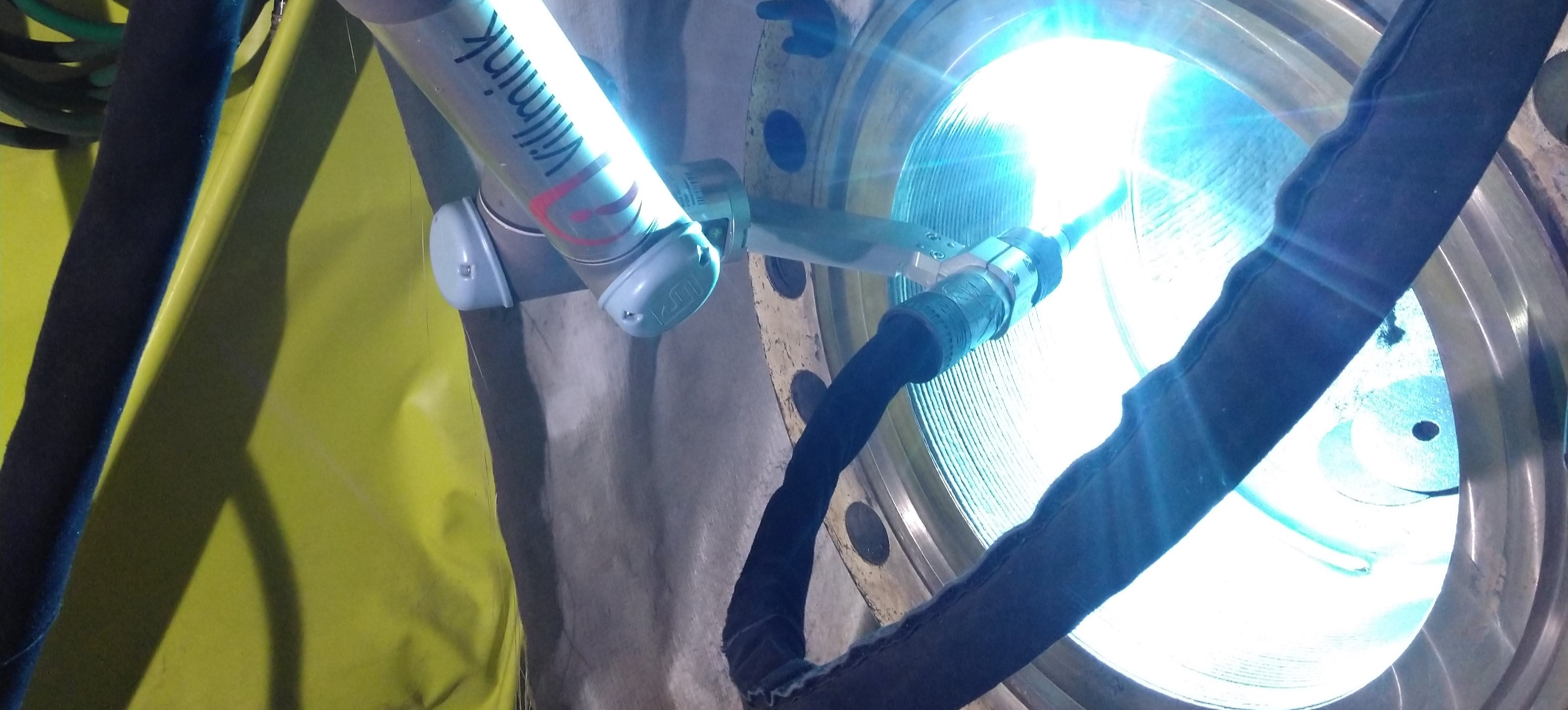
Never heard of anyone doing a similar operation
Offering increased speed, enhanced safety and better quality, robot welding is making big strides forward. Large and time-consuming repair operations can now be carried out on-site rather than on land, with equipment and service personnel transported out to the platform. The robotised technology offers substantial efficiency gains in maintenance operations, and Effee Induction is at the forefront of the development.
Effee created history in the late autumn of 2022 when it performed a golden weld operation for Equinor using a robot. This involves a higher level of inspection, yet without opportunities for post-weld pressure testing – allowing the equipment to return to work at once.
“We’ve never heard of anyone doing a similar operation before,” says Roy André Oddan, site manager for Effee Induction.
Adopting new technology
Equinor alone accounts for about 70 per cent of Norway’s offshore energy production, creating huge value daily. The production scale also generates a big demand for maintenance and repairs.
Over several years, Equinor has invested time and money in development and collaboration with players who can enhance such work and improve its health, safety and environmental (HSE) aspects. That was also the cradle for the collaboration with Effee Induction on robot welding and on-site repair.
Stringent standards
Last autumn, Equinor decided that a heat exchanger on one of its platforms had to be repaired. Corrosion damage required the replacement of two 20-inch flanges. The internal corrosion-resistant cladding had worn off and rewelding was required. Robots were to do all the work.
Repairing the corroded flanges involved a golden weld, and stringent standards were thereby set. These included more inspection and non-destructive testing (NDT).
Such an operation had not been done before, so it was preceded by much development work. Effee Induction made extensive and time-consuming preparations which included advance testing and documentation to show that the robot welding method would function. This process took several months, with efficiency and safety centre stage in the planning.
Substantial HSE gain
Few things are more important for the offshore sector than HSE. With demanding working conditions and complex operations, safety is a crucial factor and given high priority. Effee Induction could achieve a substantial gain in this respect.
While the robot performed the actual welding job, the company’s specialists supervised the work and ensured that it progressed as planned. That had clear HSE advantages, observes Frants Poulsen, head of welding technology at Effee Induction.
“Instead of manually doing a demanding welding job for hours, our specialists can be used for planning, logging and monitoring. That prevents hard wear on both knees and shoulders and ensures good control of the whole operation.”
In addition to the HSE benefit, the robot technology proved more stable than manual welding. Careful planning and programming reduced the risk of human error along the way.The robot is also highly efficient and does the job without a break – unlike a welder who naturally needs to take pauses and to reposition themselves as the work progresses.
Unique expertise and experience
Unforeseen changes naturally arise during a complex operation offshore. That also applied to the Effee Induction job, with the operation needing to be suspended several times because of weather, wind and demanding working conditions.
Nevertheless, the operation proved very successful and marked a major milestone for Effee Induction and the experience has given the company a big lead in further work on robotised welding technology.
“This operation has provided us with unique experience and expertise which we’ll take with us,” says Poulsen. “We now also possess operational data which can help to optimise future maintenance and welding work, and we can continue to build our expertise on this basis.”